It's hard to imagine a time when glass wasn't a part of everyday life, but for centuries glassmaking techniques were a carefully guarded secret and they still are. But we would like to give you a glimpse into the minds of the people who guard those secrets and give you an idea how they make their art come to life.
There are many types of glass, but the most common ones used in art are soda-lime glass, often called "Soft Glass," and borosilicate glass, often called "Hard Glass." Soda-lime is the most widely used type of glass. It is standard for windowpanes and glass containers, such as bottles and jars. Borosilicate is more of a specialty glass. It’s used extensively in the glass blowing process known as lamp working and has a higher melting point than soda-lime glass. Though more difficult to make than traditional glass, the refractory properties and physical strength of borosilicate glass make it ideal for use in high-durability laboratory equipment such as beakers, test tubes and more common items like cookware and
telescope mirrors.
Borosilicate glass is even used to contain radioactive wastes for disposal with a process called “vitrification.”
There are several different techniques and ways of working with either glass to produce sculptures, jewelry or two-dimensional artworks. Specific approaches include: working glass at room temperature, known as cold working; glass casting; fusing glass; stained glass; lampworking; and most notably, glass blowing.

“Cold Working” techniques can be used for hard glass or soft glass such as sandblasting, cutting and polishing (uses diamond blades). Etching the finished piece with acid will leaves a matte finish or an artist can engrave it by hand using diamond wheels.
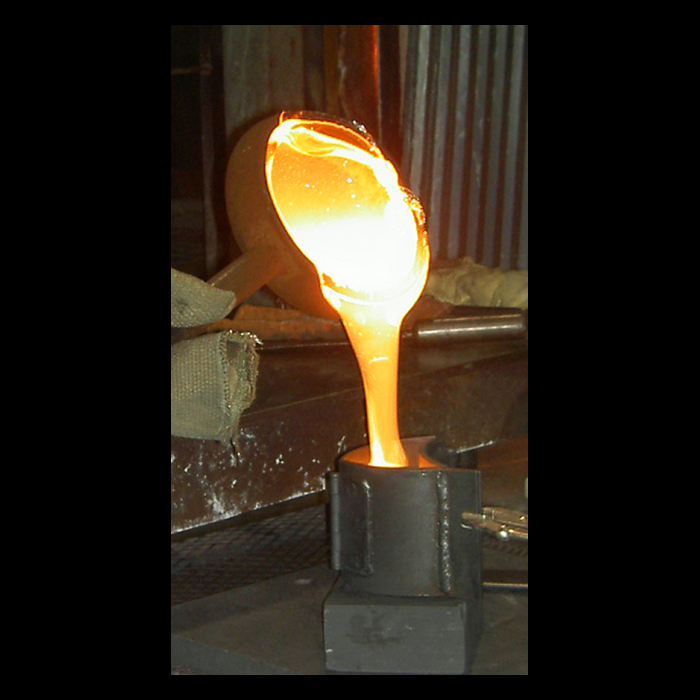
“Glass Casting” uses soft glass and can be done at the furnace, on a torch, or in a kiln. Generally, the artist makes a mold out of refractory sand, or plaster and silica. Which can be filled with either clear glass or colored or patterned glass, depending on the techniques and effects desired. Large scale sculpture is usually created this way.

"Fused Glass" the term is used to describe soft glass that has been fired in a kiln at temperatures from 1,099 °F to 1,501 °F to bond glass together. Most fusing methods involve stacking or layering thin sheets of glass, often using different colors to create patterns or simple images. The stacks of glass are then placed inside the kiln and heated until the separate pieces begin to bond together, eventually softening and rounding the edges of the original shape. While fused glass techniques are generally used to create glass art, glass tiles and jewelry, the slumping process allows the creation of larger, functional pieces like dishes, bowls, plates and ashtrays. Producing functional pieces generally requires two or more separate firings. One kiln cycle fuses the glass, followed by another that allows it to slump (bow or warp).

“Stained Glass” the artist cuts the glass into specific patterns to make their artwork. The pieces are stuck together using lead came and solder. They can also use techniques in a kiln to create texture, patterns, or change the overall shape of the glass using heat.
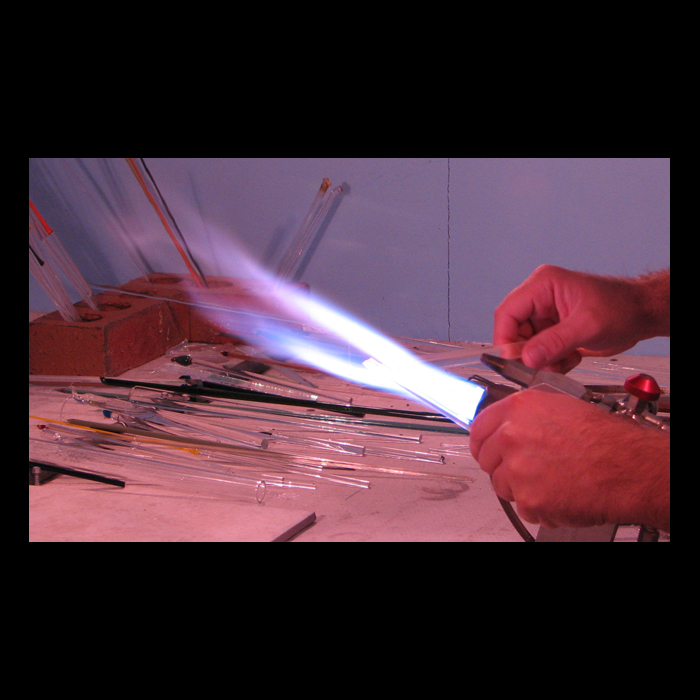
"Lamp working" the term is used to describe glass that has been heated and manipulated by using propane/oxygen torches. These torches can reach temperatures, as high as 5300 degrees Fahrenheit. The artist generally works at a bench using rods and tubes of glass, shaping with variety of metal and graphite tools but the most important one is gravity. Though the artist is somewhat limited in size, a greater level of detail can be achieved with this technique.

"Glass blowing" or "Hot Glass." Working with soft glass this way involves three furnaces and the use of a blowpipe that is dipped into the first furnace, containing a crucible of molten glass (around 2000 °F). It’s gathered on to the blowpipe in much the same way that honey is picked up on a dipper. Now they can manipulate the glass into a base shape and inflate it into a vessel. If they need to reheat a piece in between steps they will use the second furnace called the "glory hole." The final furnace is called a kiln or annealer, which is used to slowly cool the glass. This keeps the glass from cracking due to thermal stress. This technique can be used to make medium to very large works of art and functional pieces like vases, bowls and sinks.

"Annealing", is done in a kiln and in glass terms, is heating a piece until its temperature reaches a stress-relief point, that is, a temperature at which the glass is still too hard to deform, but is soft enough for internal stresses to ease. The piece is then allowed to heat-soak until its temperature is uniform throughout. The time necessary for this depends on the type of glass and thickness of the thickest section. The piece is then slowly cooled at a predetermined rate until its temperature is below a critical point, at which it can't generate internal stresses, and then can safely be dropped to room temperature. This relieves the internal stresses, resulting in a piece which should last for many years. Glass which has not been annealed may crack or shatter due to a seemingly minor temperature change or other shock.